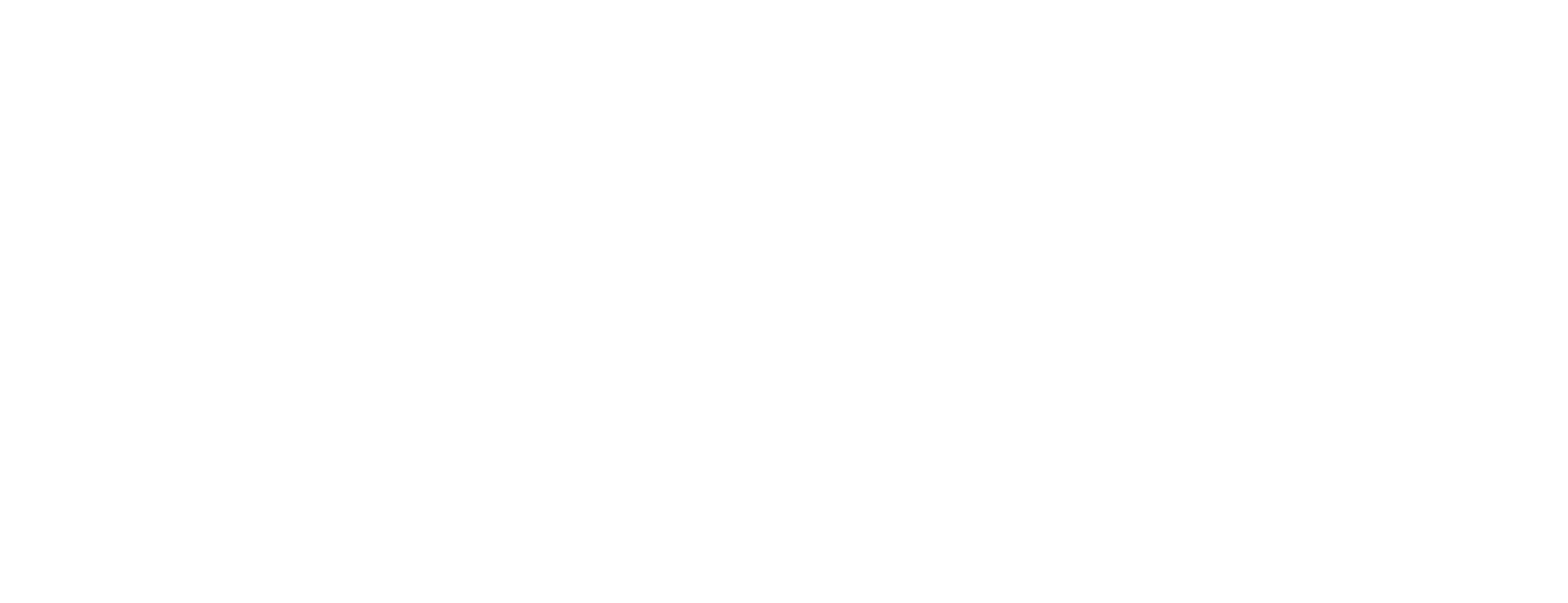
EdenCrete in prestressed concrete:
Bridging to greater efficiency and profitability
Approved for use in bridge beams by the Texas Department of Transportation, EdenCrete’s proprietary formula is beginning to transform the precast concrete industry through shortened production schedules, lower costs and more durable construction.
Pour one day, release the next
Typically, a manufacturer hopes to achieve the specified release strength in approximately 16 to 24 hours, allowing for the removal of formwork and inducing stress in the concrete members. Adding EdenCrete enables the concrete to harden more quickly and achieve the specified release strength sooner, so a factory can turn their forms over in as little as 12 to 14 hours.
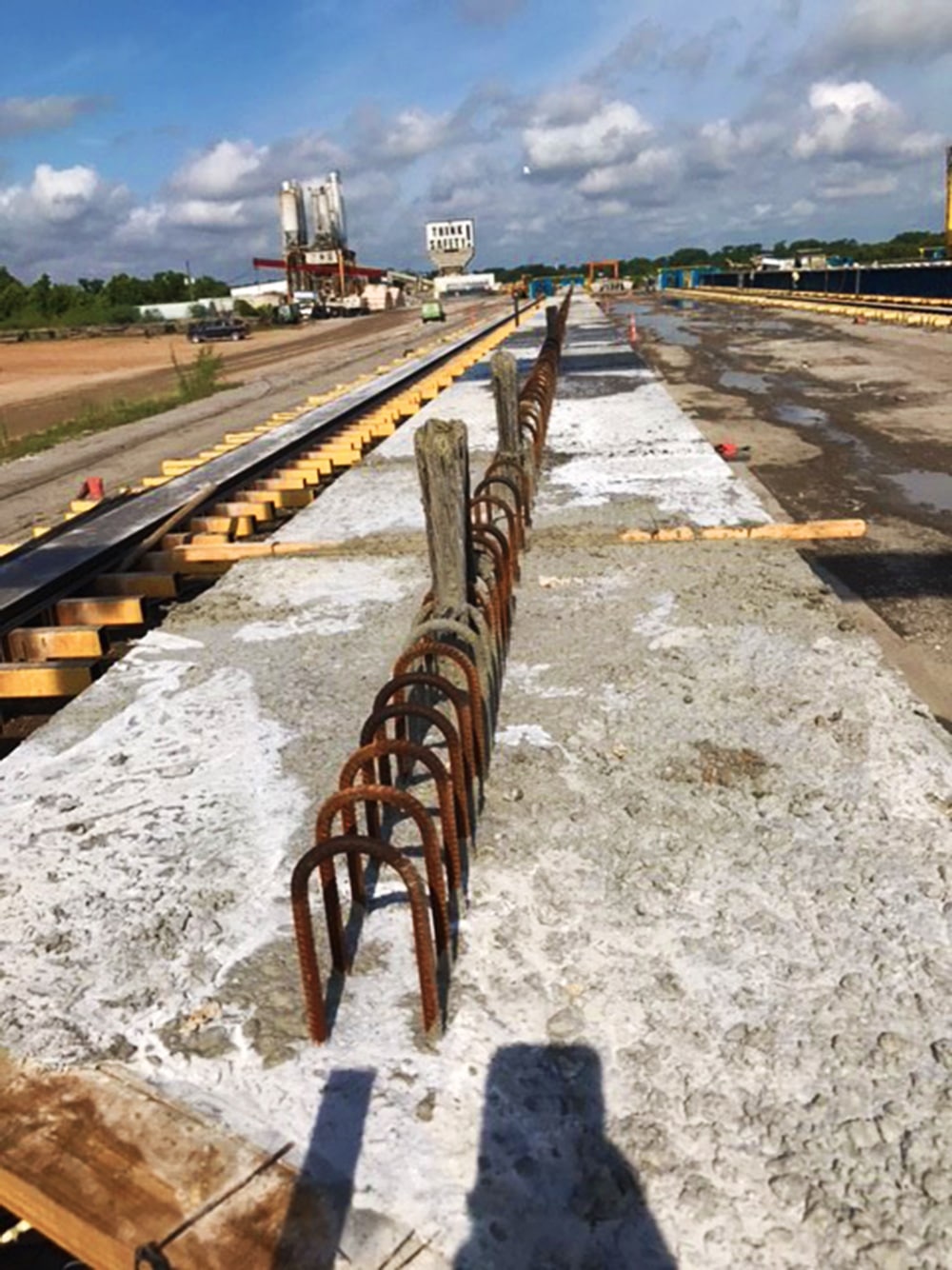
“Using EdenCrete® enables a manufacturer to lower the cement content and reduce costs without sacrificing strength and performance.”
More EdenCrete, less cement
Using EdenCrete® enables a manufacturer to lower the cement content and reduce costs without sacrificing strength and performance. The concrete will achieve stripping and design strengths more quickly, with a smoother, more attractive finish that is highly resistant to abrasion, cracking, stains and water permeability. This multi-faceted durability has been tested through extensive research and development, laboratory experiments and field trials in various environments.
Using less cement also means a greener footprint – by indirectly causing the release of less carbon dioxide into the environment.
Building new bridges
As the enriched concrete additive of the 21st century, EdenCrete® is a transformative material to the concrete industry and will have an enduring impact on a multitude of concrete applications.
With each bridge built using EdenCrete®, the industry is literally building a new bridge between the past and the future of precast concrete manufacturing processes – one durable beam at a time.
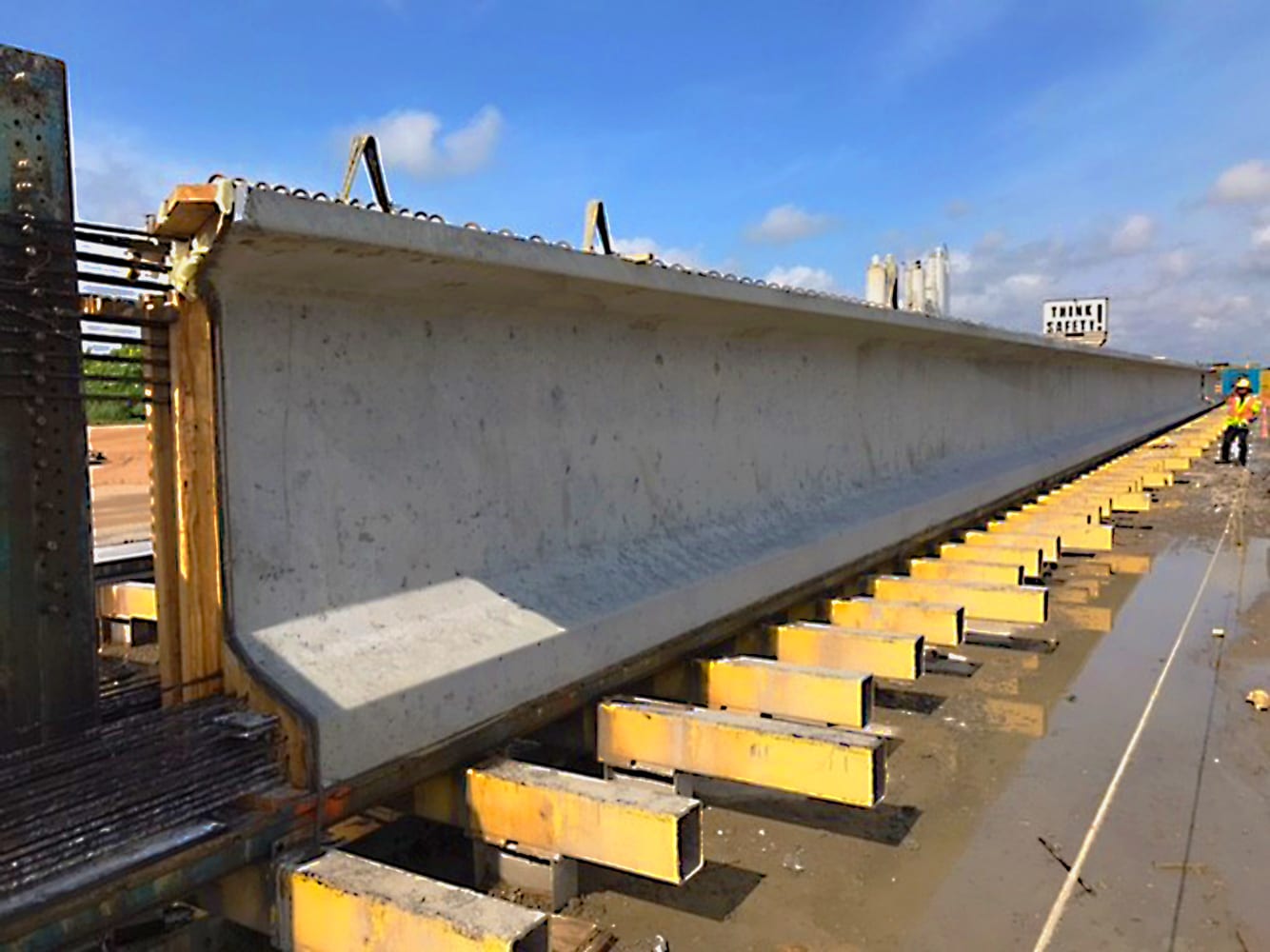
See how EdenCrete has proven its strength.
Click Below to view our case studies and see how EdenCrete® showed significant increase in key concrete attributes such as Permeability, Flexural, and Abrasion.